Cracking the Capsule Code: Radical Shifts in Fiber Capsule Manufacturing
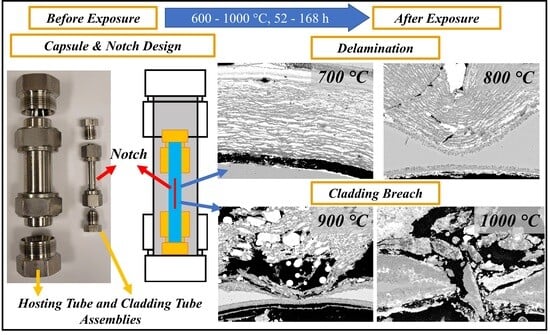
What used to be a straightforward pharmaceutical form is undergoing serious transformation. We’re talking about fiber capsule manufacturing, a domain that once leaned heavily on gelatin and cellulose but is now being pushed to the limits by science, demand, and ethics.
With the supplement market ballooning—expected to surpass $300 billion globally by 2030—innovation in how those supplements are delivered has become just as important as the formulas themselves.
Let’s not sugarcoat it. Traditional methods have hit their ceiling. You’ve got animal-based gelatin caps that clash with vegan preferences. HPMC (hydroxypropyl methylcellulose) filled the gap, but it’s got its own baggage—solubility issues in low-moisture environments, delayed disintegration times, and a laundry list of additives that make clean-label purists cringe.
So, where are we headed?
Fermentation-Based Alternatives: Biotech Enters the Chat
Startup labs and large manufacturers alike are banking on microbial fermentation. Instead of extracting cellulose from wood pulp or growing gelatin from animal collagen, scientists are teaching microbes to produce fibrous polymers. It’s eerily similar to how we brew beer—only instead of hops, the endgame is a plant-like shell that dissolves smoothly in your stomach.
What’s wild is the efficiency. One company in Europe claims its fermentation-grown fiber capsule tech reduces water use by over 70% compared to HPMC manufacturing. Plus, you can engineer these fibers at the molecular level. Want a slower release rate for those sleep supplements? Done. Need them to dissolve in alkaline conditions? Tweaked with a minor change in pH during production.
Smart Capsules: Not Sci-Fi Anymore
Some researchers are going full Tony Stark on capsule design. We’re now seeing developments in encapsulation that respond to your body’s internal cues. Imagine a capsule that holds its form until it detects specific enzymes in your gut. Or one that bypasses your stomach entirely and only releases nutrients once it hits the small intestine.
It’s not science fiction. In Japan, drug delivery systems are being tested using pectin-coated fibers that degrade only under certain microbial conditions. This precision helps protect sensitive compounds like probiotics and omega fatty acids, which would otherwise break down before they’re absorbed.
Clean Label: The Holy Grail (And the Minefield)
Here’s the paradox: consumers want transparency, but also peak performance. That creates a headache for manufacturers. You can’t just slap “all-natural” on a product and pray it works like the synthetic version.
There’s been a resurgence in interest around seaweed-based fibers, like alginate and carrageenan. These marine biopolymers are rich in polysaccharides and can form stable capsules without chemical crosslinkers. Sounds great—until you realize sourcing is seasonal, yields vary wildly, and not everyone’s keen on that oceanic aftertaste. Still, companies are investing because these options offer both sustainability and traceability.
Speed, Scalability, and Cost: The Trifecta Challenge
Here’s where things get gritty. Innovative materials sound great on a TED Talk stage, but how do you scale them to 50 million capsules a week? Automated capsule-filling machines are often finicky. They were designed decades ago with gelatin in mind. Switch the material, and suddenly you’re getting jams, crumbling, or capsules that don’t seal properly.
Enter 3D-printed molds and adaptive machinery. Forward-thinking manufacturers are developing systems that adjust in real time based on fiber viscosity and capsule weight. Think of it like a self-tuning piano that keeps playing in perfect pitch—even if you change the strings mid-song.
But it’s not cheap. Retooling a factory for fiber capsule innovation can run into the millions. Smaller companies often license tech from bigger players or use third-party manufacturers to cut upfront costs.
Sustainability: Beyond Buzzwords
Let’s call out the elephant in the room. Eco-friendly doesn’t mean much if your entire production line is guzzling electricity and spitting out waste. That’s why some of the most promising work isn’t in the capsule itself, but in the supply chain.
Case in point: agricultural waste being repurposed as raw material. Corn husks, pineapple leaves, even sugarcane bagasse are now being processed into fibrous inputs for capsule production. It kills two birds—reduces landfill waste and creates a low-cost, plant-based source of material.
Then there’s lifecycle analysis. Some manufacturers now publish full reports showing carbon impact per capsule. It’s a game-changer for brands trying to prove their sustainability claims.
What Consumers Don’t See (But Definitely Feel)
Let’s take a second to talk about user experience. It’s subtle but real. Ever tried a supplement and felt bloated or “off” even though it was all-natural? The culprit might not be the ingredients, but the capsule shell.
Certain fiber capsules interact with stomach acid differently. Some trap air. Some draw in too much moisture. Others degrade unevenly. The result? Gassy discomfort or slower nutrient uptake.
Newer innovations address this by adding plant-based emulsifiers or air-expelling techniques during filling. It’s the kind of thing you don’t read on the label, but your gut knows.
Final Thoughts? Scratch That.
Capsule innovation isn’t just a story for pharma nerds and factory engineers. It impacts everyone popping a vitamin before bed or chasing energy with a morning booster. As science continues to push the boundaries—through fermentation, smart release, biodegradable sources, and AI-driven manufacturing—we’re inching closer to capsules that are smarter, safer, and way more sustainable than their predecessors.