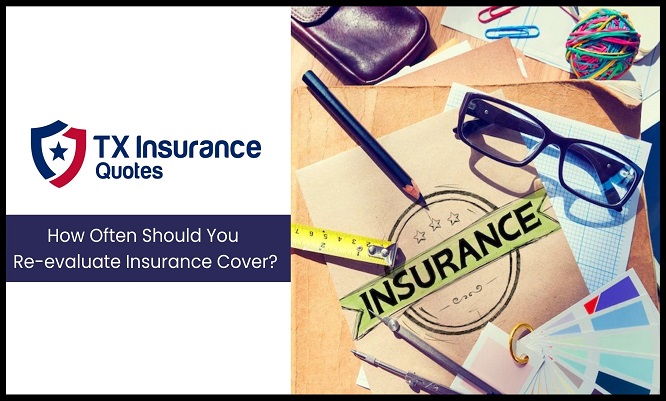
It’s best to check your insurance policy coverage at least once a year to ensure your family and valuables are adequately protected. When you’ve made a significant purchase or experienced a major life event such as getting married, buying a house, sending your kid to college, or receiving an inheritance, it’s time to review your coverage. These life events are considered insurance-qualifying occurrences, and it’s critical to make sure your coverage is up to date to safeguard the people and things that are most important to you.
Reviewing your insurance coverage is an easy way to ensure that you and your family are protected from accidents, theft, or natural disasters. By taking the time to understand your policy and make sure it’s up to date, you can rest assured that you’re prepared for whatever life throws your way. Also, your homeowner’s insurance companies will provide an annual review of your policy to make sure you’re still adequately covered.
What Is an Insurance Review?
A review of your insurance coverage entails looking at your insurance policy covers, including automobiles, property, family members, and other valuables. To learn more about your insurance coverage, contact an experienced homeowners insurance agent in El Paso to utilize their experience and knowledge. An agent can help you understand your policy, identify any gaps in coverage, and make recommendations to protect your family and possessions best.
The Benefits of an Insurance Review
There are several benefits to conducting an annual review of your insurance coverage. But, perhaps the most crucial advantage is that it gives you peace of mind. By analyzing your coverage, you can be sure that you and your family are adequately protected in an accident, theft, or natural disaster.
Another benefit of an insurance review is that it can help you save money on your premiums. By understanding your coverage and making sure that you have the right amount of coverage for your needs. You can avoid paying for coverage that you don’t need. This can help keep your premiums affordable and give you more financial flexibility in an emergency.
Finally, an insurance review can help you to be prepared for the future. By understanding your coverage and making sure it’s up to date. You can be sure that you’re prepared for whatever life throws your way. This peace of mind is priceless and can help you focus on the most important things to you.
Why and When Should You Review Your Insurance Coverage?
It is critical to check your insurance coverage regularly to guarantee that your property, valuables, and loved ones are adequately protected. Consider your home insurance (or renters insurance), auto insurance, and any other policies in your name during an insurance review. Also, if you’ve made a significant purchase or experienced a major life event. It is essential to check your coverage to ensure that you’re still adequately protected.
When should a review be done? If your possibilities change, or you have a “qualifying occurrence” or a “life-changing event”. You may wish to have your insurance reviewed. Qualifying occurrences are changes in your life that can impact your insurance needs. Such as getting married or divorced, having a baby, moving to a new home, or taking out a mortgage. Life-changing events are major changes that can impact your ability to pay for insurance. Such as a job loss, serious illness, or the death of a family member.
It’s also a good idea to review your coverage annually. Even if you don’t have a qualifying occurrence or life-changing event. This is because your needs can change over time, and it’s important to make sure that your coverage is still adequate. For example, if you’ve made a significant purchase, such as a new home or car. You’ll need to ensure that your coverage reflects the new value of your possessions.
If you are not sure if you need to review your insurance coverage, contact an experienced homeowners insurance agent in Beaumont. They can assist you in comprehending your insurance and making suggestions for how to best safeguard your family and belongings.
What Does It Mean to Be an Insurance-Qualifying Event?
An insurance-qualifying occurrence is an event that alters your life circumstances. Because these occurrences might happen throughout an insurance policy, you’ll want to contact your agent if one occurs outside of the usual policy renewal deadline.
A qualifying or life-changing occurrence, for insurance purposes, is typically defined as:
- The status of your family: This includes having a kid, adopting a youngster, getting married, getting divorced, or losing a family member.
- Childhood milestones: It’s a good time to contact your insurance agent when your youngster graduates from school, goes off to college, turns 16, and is allowed to drive.
- Retirement and aging milestones: An insurance evaluation may assist you in determining whether your insurance coverage requires updating if you retire and no longer commute to work or downsize from owning a house to renting one.
- Changes in the workplace: If your firm is changing, you may also need to get your insurance evaluated. These events might include selling your company, going public with an Initial Public Offering (IPO), or relocating offices.
- Changes in your living situation: Selling your home, buying a new one, or moving to a rental property are all life changes that can impact your insurance needs.
Significant events are unavoidable. You can concentrate more on the essential things in life when your insurance coverage is linked to your life events.
Other Times You Might Want an Insurance Review
In addition to the major life changes and milestones that we’ve already discussed. There are other times when you may want to consider an insurance review. For example, if you’ve made a large purchase, such as a new home or car. You’ll want to update your insurance coverage to reflect the new value of your possessions.
Suppose a natural disaster has recently struck your areas, such as a hurricane, tornado, or wildfire. In that case, you may want to review your homeowner’s insurance policy. To ensure that you have the coverage you need to rebuild your home if it’s damaged or destroyed.
Check with your homeowner’s insurance in Harlingen for more information on how often you should review your policy.
How Often Should You Change Your Coverage?
It’s good to review your insurance coverage at least once a year. Even if you don’t have a qualifying occurrence or life-changing event. But that does not always mean you will have to make adjustments regularly.
In many cases, your current insurance may still be sufficient. However, it’s a good idea to go over all of your insurance requirements. At least once a year in most cases. Contact your homeowner’s insurance agent in Victoria or company representative if you have a significant life change.
Read here: Complete understanding on home insurance vs life insurance.
In Conclusion
There is no set time frame for how often you should review your insurance coverage. However, it’s usually a good idea to do so at least once a year or after any major life changes. If you’re not sure whether or not you need to review your insurance coverage, contact an experienced homeowners insurance company agent. They can help you understand your options and make the best decision for your needs.